In the world of manufacturing and processing industries, efficient and accurate sieving is a crucial step in ensuring product quality and consistency. The screen mesh size plays a pivotal role in determining the effectiveness of the sieving process, as it directly affects the particle size distribution and overall performance of the operation. In this article, we delve into how screen mesh size influences the quality and performance of industrial sieving processes and its significance in various sectors.
One of the primary functions of industrial sieving is to separate particles based on their size. The mesh size, represented by the number of wires per inch or the size of the openings, directly determines the size of particles that can pass through the screen. Finer mesh sizes allow only smaller particles to pass through, resulting in a more precise separation. In contrast, coarser mesh sizes permit larger particles to pass, potentially leading to a less accurate separation. For example, in the pharmaceutical industry, where precision and consistency are paramount, a finer screen mesh is essential to ensure that only uniform-sized particles are used in drug formulation and manufacturing processes. On the other hand, in the agricultural sector, coarser screen mesh is used for grain cleaning to remove larger impurities, while allowing smaller grains to pass through.
The screen mesh size significantly influences the sieving throughput and overall efficiency of industrial processes. Finer mesh sizes often lead to slower throughput due to increased resistance to particle passage. Conversely, coarser mesh sizes facilitate higher throughput but may compromise separation accuracy.
Manufacturers must strike a balance between throughput and accuracy, considering the specific application and production requirements. A thorough understanding of the material being processed and the desired outcome is essential in selecting the most appropriate screen mesh size.
Apart from the mesh size, the choice of screen mesh material is equally important. Various materials, such as stainless steel, brass, and synthetic fabrics, are used in screen manufacturing, each offering unique properties in terms of strength, durability, and resistance to corrosion or wear.
In heavy-duty industries like mining and construction, where the sieving equipment is subject to harsh conditions and abrasive materials, durable screen mesh materials with larger openings are often preferred to ensure longevity. Conversely, in the food and pharmaceutical sectors, where hygiene is critical, stainless steel or nylon mesh with finer openings are chosen to prevent contamination and meet regulatory standards.
The screen mesh size can have a direct impact on the quality of the final product. In industries like ceramics, where particle size distribution affects the properties of the end product, using the right screen mesh size is essential to achieving the desired characteristics such as strength, color, and porosity.
For instance, in the manufacturing of powdered milk products, a precise and consistent particle size distribution achieved through the use of specific screen mesh sizes ensures a uniform texture and enhanced reconstitution properties in the final product.
The choice of screen mesh size also affects energy consumption during sieving processes. Finer mesh sizes require more energy to push particles through the screen due to increased resistance. This can result in higher operating costs in large-scale industrial operations. On the other hand, coarser mesh sizes demand less energy for the sieving process, leading to potential cost savings. However, it is essential to strike a balance between energy consumption and the desired outcome of the sieving process to optimize overall efficiency.
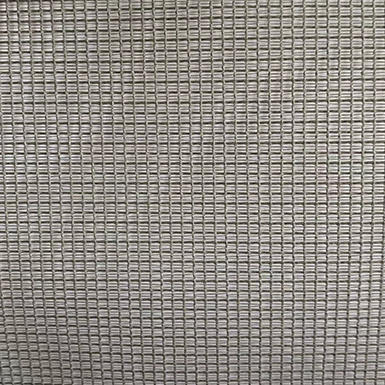
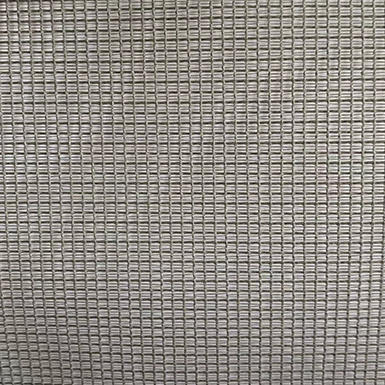